Regulación y Control de Instalaciones Frigoríficas
Equilibrio en el sistema frigorífico
Cuando se diseña un sistema frigorífico hay que tener en cuenta que los elementos que lo componen, compresor, condensador y evaporador, están continuamente interaccionando entre sí. Esa interacción llevará automáticamente a una situación de equilibrio, de forma que la cantidad de Kg/h que se vaporicen será igual a la cantidad de kg/h que trasiegue el compresor, para una determinada temperatura de condensación.
Si el evaporador y el compresor no tienen la misma capacidad correspondiente a las condiciones de diseño, el punto de equilibrio ocurrirá en otras condiciones distintas a las esperadas.
El evaporador (manejando líquido saturado) aumenta su efecto frigorífico al descender la temperatura de evaporación (manteniendo una determinada temperatura de condensación). Sin embargo, el compresor aumenta su potencia frigorífica al aumentar la temperatura de evaporación. No obstante, para unas condiciones dadas, las potencias frigoríficas del evaporador y el compresor se equilibran en un punto, donde ambos tienen la misma potencia. Este punto de equilibrio se puede determinar de la forma siguiente. Primero, y para una determinada temperatura de condensación, se construyen, según datos de catálogo, las curvas:
1) potencia evaporador = f(temperatura de evaporación)
2) potencia compresor = f(temperatura de evaporación)
El punto de intersección de las dos rectas será el punto de equilibrio, no teniendo en cuenta las posibles pérdidas de carga en el circuito frigorífico.
Al variar la temperatura de condensación variará el punto de equilibrio, de forma que al aumentar esa temperatura disminuye la potencia del sistema frigorífico.
Cuando se resuelve una determinada instalación frigorífica, la determinación de estas curvas nos indicará si el punto de equilibrio se aleja más o menos de nuestras condiciones de diseño.
Funcionamiento cíclico del sistema frigorífico
En general, el sistema frigorífico no funcionará continuamente. En efecto, si el compresor siguiera funcionando una vez conseguida la temperatura de régimen en un recinto enfriado, podría disminuir esa temperatura, con posibles efectos perjudiciales sobre el producto conservado.
La instalación frigorífica se diseñará para afrontar satisfactoriamente la máxima carga térmica del sistema, pensando que tendrá un tiempo máximo fijado de funcionamiento al día. El resto del tiempo el equipo estará desconectado.
Así, pues, el funcionamiento del equipo frigorífico será una sucesión, controlada automáticamente, de ciclos desconectar y conectar. En situación de carga térmica punta, los ciclos conectar serán más largos que en los períodos de carga mínima.
Los automatismos usados para ciclar un sistema frigorífico, asegurando su adecuado funcionamiento, son de dos tipos principalmente:
1) controles termostáticos,y
2) controles presostáticos.
Sistemas de control automático
Estos sistemas se componen de : (1) transductor (elemento primario), (2) detector de error o regulador y (3) elemento final de control o actuador. El transductor es un convertidor de señal de una forma a otra (por ejemplo, recibe temperatura y la transmite como presión). No hay que confundir entre sensor y transductor: el sensor, que forma parte del transductor, es el elemento que capta la señal; el transductor es el elemento que realiza la función explicada anteriormente. El regulador compara el valor consigna con el detectado por el transductor y comunica esa información al elemento final de control, por medio de una salida con suficiente potencia. El actuador trata de corregir el error detectado en la medida de la variable controlada, modificando la posición de una válvula, accionando o parando un motor, etc
En un sistema de control se tiene el ajuste de diferencial y el ajuste de punto de consigna. El ajuste diferencial indica el margen de variación de la variable controlada. El punto de consigna es el valor de la variable controlada, que deseamos tener. El sistema de control automático ha de llevar al sistema frigorífico a ese punto de consigna. Por ejemplo, el punto de consigna podría ser la temperatura de fermentación de un mosto blanco en la elaboración de vino y podría fijarse el ajuste diferencial de forma que esa temperatura de fermentación no variase más de ±0,5 ºC. Los automatismos pueden conseguir el buen funcionamiento del sistema frigorífico en otras condiciones a las de equilibrio, dándole por tanto una cierta flexibilidad.
Los sistemas de control termostático utilizan como sensores elementos sensibles a la temperatura, tales como (1) la lámina bimetálica, (2) sonda con vástago y tubo, (3) y sonda de fuelle o sonda con bulbo, tubo capilar y fuelle. La lámina bimetálica está construida con dos metales de diferentes coeficientes de dilatación. Un cambio de temperatura provoca una curvatura de la lámina. Este movimiento es detectado por el regulador. La sonda con vástago y tubo se basa en que el tubo tiene un coeficiente de dilatación mayor que el vástago, con lo cual un cambio de temperatura provoca un movimiento del vástago. Las sondas de fuelle contienen un fluido (líquido, vapor o gas) que se dilata o contrae con los cambios de temperatura, provocando el movimiento del fuelle. Cuando el sensor ha de estar alejado del fuelle se utiliza un capilar de unión bulbo-fuelle.
En sistemas de control termostático electrónico, se pueden utilizar como transductores sondas de resistencia y termistores. Las sondas de resistencia sufren una variación de resistencia de un conductor (níquel, platino) con el cambio de temperatura. Los termistores son semiconductores electrónicos con un coeficiente de temperatura de resistencia negativo de valor elevado. Estos semiconductores también padecen una variación de resistencia al modificarse la temperatura.
Los elementos primarios en sistemas de control de presión están constituidos principalmente por un fuelle o un diafragma. Las variaciones de presión, transmitidas por medio de un capilar, provocan el alargamiento del fuelle o la flexión del diafragma.
En los sistemas de control mecánicos, un cambio de la variable controlada (presión, temperatura) se refleja en el movimiento de unas palancas, que pueden abrir o cerrar un interruptor, variar la resistencia por medio de un potenciómetro, o accionar una válvula que modifica la presión en un actuador neumático.
Cuando el sistema de control es electrónico, el transductor convierte la señal de temperatura en señal eléctrica. La ventaja de las señales eléctricas es su facilidad para ser almacenadas, amplificadas o tratadas (ecualización, rectificación, etc).
Ciclado del sistema
Los sistemas de control de presión, de ciclado del compresor, son de presión alta y presión baja. El control de presión alta es un control de seguridad, y se conecta en la tubería de descarga del compresor. Desconecta el compresor cuando la presión en el lado de alta es demasiado grande.
Los controles de presión baja se usan tanto en controles de seguridad como en controles de la temperatura. Interrumpen el circuito (se para el compresor) cuando la presión en el lado de baja está por debajo de cierto límite. Conectan el motor del compresor cuando la presión en el lado de baja es normal.
A medida que el evaporador se calienta durante el ciclo de parada, se aumenta también la presión en el evaporador, hasta la correspondiente a la de arranque del compresor.
Debido a que el vapor refrigerante sufre una caída de presión mientras circula por la tubería de aspiración, la presión a la entrada del compresor es por lo general de 0,14-0,21 kg/cm2 menor que la presión en el evaporador. Esto ha de tenerse en cuenta a la hora de regular el presostato de baja (sólo la presión de desconectar, pero no la de conectar).
Como el control de presión baja regula o controla la temperatura del evaporador más que la temperatura de la cámara, resulta un control de temperatura ideal para aplicaciones que requieran ciclos de paro para efectuar deshielo (desescarche). Esto es muy adecuado sobre todo para instalaciones "remotas", donde el compresor está localizado lejos del evaporador.
Otras veces la temperatura del espacio refrigerado o la del evaporador es controlada termostáticamente. Según sea la temperatura, se actúa para abrir o cerrar una válvula solenoide instalada en la tubería de líquido, cerca de la válvula de expansión. Cuando la temperatura baja hasta la temperatura de "desconectar" se cierra la electroválvula de paso de líquido hacia el evaporador. El compresor sigue funcionando hasta que la presión dentro del evaporador baja hasta la presión de "desconectar", actuando el control de baja parando el compresor.
Cuando la temperatura del evaporador aumenta hasta la de "arrranque", el termostato deja abrir la válvula de solenoide dejando pasar líquido refrigerante al evaporador. Como éste está caliente, el líquido se vaporiza rápidamente aumentando la presión hasta la presión de "arranque" del compresor accionado por el presostato.
Control de la capacidad frigorífica
El sistema frigorífico ha de ser diseñado para tener una capacidad igual o ligeramente mayor a la carga promedio máxima. Así, el equipo tendrá capacidad suficiente para mantener la temperatura y la humedad en los niveles deseados durante los períodos de carga punta.
Mientras los cambios en la carga promedio del sistema no sean grandes, el control de la capacidad se logra simplemente ciclando el sistema de arranque y paro. Estos ciclos variarán de acuerdo con la carga que se tenga en la cámara.
Pero cuando los cambios en la carga del sistema son grandes, es necesario prever algunos medios de variación o regulación, automática o manual, de la capacidad del equipo diferentes al sistema del ciclado arranque-paro.
Cuando se desee variar la capacidad del sistema sin permitir cambios en las condiciones de operación del mismo será necesario controlar directamente tanto la capacidad del evaporador como la del compresor.
Mientras los cambios en la carga promedio del sistema no sean grandes, el control de la capacidad se logra simplemente ciclando el sistema de arranque y paro. Estos ciclos variarán de acuerdo con la carga que se tenga en la cámara.
Pero cuando los cambios en la carga del sistema son grandes, es necesario prever algunos medios de variación o regulación, automática o manual, de la capacidad del equipo diferentes al sistema del ciclado arranque-paro.
Cuando se desee variar la capacidad del sistema sin permitir cambios en las condiciones de operación del mismo será necesario controlar directamente tanto la capacidad del evaporador como la del compresor.
Mientras los cambios en la carga promedio del sistema no sean grandes, el control de la capacidad se logra simplemente ciclando el sistema de arranque y paro. Estos ciclos variarán de acuerdo con la carga que se tenga en la cámara.
Pero cuando los cambios en la carga del sistema son grandes, es necesario prever algunos medios de variación o regulación, automática o manual, de la capacidad del equipo diferentes al sistema del ciclado arranque-paro.
Cuando se desee variar la capacidad del sistema sin permitir cambios en las condiciones de operación del mismo será necesario controlar directamente tanto la capacidad del evaporador como la del compresor.
Control de la capacidad del evaporador
El método más efectivo es el de dividir el evaporador en varias secciones o circuitos separados, los cuales podrán ser controlados por separado, de tal forma que una o más secciones o circuitos puedan eliminarse cuando disminuya la carga.
La disposición de los circuitos puede diseñarse, ya sea para controlar el área frontal o el área en profundidad del evaporador, o bien para ambas.
Otro método común de cambiar la capacidad del evaporador es variando la cantidad de aire circulado sobre el mismo, utilizando para ello compuertas frontales o de desviación.
Para casi todos los casos anteriores se necesita simultáneamente controlar la capacidad del compresor.
Control de la capacidad del compresor
Un método para controlar la capacidad de un compresor alternativo podría consistir en variar la velocidad del compresor, variando la velocidad del impulsor del compresor.
Sin embargo, el control de la capacidad de un compresor de varios cilindros, se obtiene normalmente "descargando" uno o más cilindros, de tal manera que éstos se vuelven inefectivos. Un método de hacerlo es desviando la descarga de uno o más de los cilindros regresándola a la tubería de aspiración.
Cuando la presión en la aspiración baja hasta un valor determinado, una válvula de solenoide instalada en la tubería de desviación (bypass), impulsada por un presostato, abre y permite la descarga de uno o más cilindros, comunicando la descarga con la aspiración. Cuando la presión en la aspiración aumenta hasta un valor fijado, se desexcita la electroválvula y se cierra el tubo de desviación, de forma que el compresor retorna a su capacidad de completo funcionamiento.
Otro método de descargar los cilindros del compresor es abriendo las válvulas de aspiración del cilindro o los cilindros, de manera que éstas permanezcan abiertas durante la carrera de compresión. El vapor es devuelto a la tubería de aspiración.
El funcionamiento del mecanismo de descarga es como sigue: cuando baja la presión en la aspiración hasta la presión de conectar del control de la presión, éste comanda una electroválvula que deja volver vapor a presión del condensador al pistón que se quiere descargar. Este vapor actúa abriendo la válvula de admisión. Cuando aumenta la presión de aspiración hasta la correspondiente de desconexión del control de presión (presostato), la válvula de solenoide se cierra y no deja pasar vapor a presión, y el pistón descargado vuelve a su operación normal.
El gas caliente desviado (uso del by-pass) es con frecuencia el único medio para controlar la capacidad de los compresores pequeños (hasta 10 CV); es también usado para suplementar a otros métodos más eficientes de control de capacidad, en situaciones donde es necesario tener control de la capacidad hasta con 0% de carga, o para casos de arranque sin carga.
Otro sistema para controlar la capacidad del compresor es el que utiliza dos o más compresores en paralelo. Se utilizan en cada uno controles de presión baja para ciclar los compresores. Además, estos compresores suelen ir equipados con cilindros que se pueden descargar, proporcionando así una forma adicional de control. Normalmente, los sistemas de reducción de potencia frigorífica de los compresores alternativos por descarga de cilindros, no reducen en igual medida el consumo de energía eléctrica. Es decir, con estos sistemas de reducción de potencia se reduce progresivamente la potencia frigorífica específica (Kcal/Kw h) del compresor, aumentando el consumo de Kw por Kcal/h eliminada del sistema frigorífico. Por esto, es más recomendable el uso de compresores en paralelo, de cara a un mejor aprovechamiento de la energía eléctrica.
Válvulas en la instalación frigorífica
Dispositivos de expansión
(1) Válvula de expansión manual
La válvula de expansión manual es utilizada como válvula auxiliar de regulación de flujo del refrigerante, instalándose en una tubería de desviación. Con frecuencia también se usa en el control del caudal a través de tuberías de purgado o sangrado.
Son válvulas de aguja, operadas manualmente. El caudal de paso por la válvula depende del grado de apertura de la válvula y del diferencial de presión a través del orificio de la válvula.
(2) Válvulas de expansión automáticas
Se trata en este caso de válvulas de asiento de accionamiento automático. Estas válvulas se componen de un tornillo de ajuste, resorte, fuelle o diafragma, vástago y asiento
La presión constante que pueden mantener estas válvulas en el evaporador se consigue con la interacción entre la presión en el evaporador y la tensión del resorte. Cuando la presión en el evaporador disminuye por debajo de cierto valor establecido previamente (regulando el tornillo de ajuste) la válvula se abre dejando pasar líquido frigorígeno, hasta que la presión en el evaporador vuelva a subir, cerrándose entonces la válvula.
Con esta válvula, sólo se permite que una pequeña parte del evaporador esté lleno de líquido durante los períodos de elevada carga térmica. La característica de presión constante de la válvula de expansión automática limita la capacidad y eficiencia del sistema de refrigeración para la condición de capacidad alta. Además, en condiciones de carga mínima el evaporador está prácticamente inundado aumentando la temperatura en los vapores del tramo de aspiración, teniendo pérdidas de capacidad y eficiencia del compresor (que maneja vapor sobrecalentado excesivamente). Esto ocurre en los períodos de puesta en marcha del compresor.
Otra desventaja de la válvula de expansión automática es que no se puede utilizar junto con un control del compresor del baja presión, ya que en el evaporador se mantiene la presión constante.
Por todo lo anterior, la válvula de expansión automática es adecuada sólo en sistemas de carga pequeña. Pero, aun en estos sistemas es poco utilizada.
(3) Válvula de expansión termostática
Debido a sus grandes ventajas y a su fácil instalación, esta válvula es quizá la más utilizada en sistemas frigoríficos. Asegura que el vapor que se va formando en el evaporador se sobrecalienta hasta cierto nivel controlado. Esto permite mantener el evaporador completamente lleno de refrigerante bajo las condiciones de carga del sistema, sin peligro de paso de líquido a la tubería de aspiración. La denominación "termostática" puede prestarse a error, puesto que el control no se hace por la temperatura del evaporador, sino por el grado de recalentamiento del gas de admisión que sale del evaporador.
Es adecuada para la regulación de caudal de refrigerante en sistemas sujetos a amplias variaciones de carga. Se trata de una válvula de asiento accionada por la dilatación o contracción de un fluido sensible a los cambios de temperatura registrados en un bulbo. La tensión del muelle que equilibra el esfuerzo de dilatación del fluido puede ser regulada por un tornillo de ajuste.
Salvo algunas excepciones, el fluido del bulbo es el refrigerante usado en el sistema. La presión de este fluido actúa en uno de los lados de los fuelles o diafragma a través del bulbo capilar y tiende a mover el obturador abriéndolo. Pero, es la presión de interior del sistema del evaporador la que tiende a cerrar la válvula.
Para este tipo de válvula, la cantidad de sobrecalentamiento necesario para lograr el equilibrio depende de la tensión que se tenga en el resorte. Al aumentar la presión en el muelle, se aumenta el sobrecalentamiento necesario para compensar esa tensión y llevar a la válvula a la condición de equilibrio.
Normalmente, las válvulas de expansión termostática se ajustan por el fabricante para un sobrecalentamiento del orden de 7-10 ºC. Este sobrecalentamiento se mantendrá constante independientemente de las condiciones de carga térmica del evaporador. Pero, esta válvula termostática no puede mantener una cierta temperatura y presión en el evaporador, únicamente un sobrecalentamiento constante.
Como el refrigerante sufre una pérdida de carga a través del evaporador, la temperatura de saturación del refrigerante es siempre menor a la salida del evaporador que a la entrada. Cuando ese incremento de presión es grande, las diferencias de temperaturas entre la salida y la entrada también son considerables. Esto da lugar a problemas de funcionamiento de la válvula termostática. Esta necesita de un mayor sobrecalentamiento en el tramo de aspiración para conseguir que la válvula llegue al equilibrio. Este fenómeno provoca el que se necesite gran parte del evaporador (de la superficie de intercambio) para satisfacer las necesidades de sobrecalentamiento. De esta forma, el hecho de que la caída de presión sea pronunciada, tiene como consecuencia una reducción de la superficie útil del evaporador. La disposición de un compensador de presión no reduce la caída de presión en el evaporador, pero permite usar toda la superficie efectiva del evaporador. En este caso la presión que actúa sobre el diafragma de la válvula es la presión de salida del evaporador, en lugar de la presión de entrada del mismo. El tubo de equilibrio se conecta a la salida del evaporador situado a unos 20 cm de la conexión del bulbo.
Una de las desventajas de la válvula de expansión termostática es la de abrirse completamente y sobrealimentar al evaporador durante el arranque del compresor, lo cual permite a veces la entrada de refrigerante líquido en la tubería de aspiración. Esto es debido a que el bulbo se calienta durante los períodos de parada, y se tiene sobrealimentación durante el arranque hasta que el bulbo no registre la temperatura normal de funcionamiento del vapor. Estas dificultades de operación pueden paliarse usando válvulas de expansión termostáticas con dispositivos limitadores de presión. Estos dispositivos funcionan estrangulando el flujo del líquido que va hacia el evaporador, quitándole el control de la válvula al bulbo cuando la presión en el evaporador aumenta hasta un máximo determinado. Esa presión máxima puede limitarse por medios mecánicos o mediante el uso de un bulbo cargado con un gas.
Ese control de presión máxima en el evaporador hace que se demore la abertura de la válvula lo suficiente como para permitir que el vapor en el tramo de aspiración enfríe el bulbo y se reduzca la presión en el bulbo antes de que la válvula abra.
La válvula de expansión termostática cargada con gas esencialmente es una válvula limitadora de presión. El bulbo de esta válvula de expansión es cargado con gas del mismo refrigerante que tiene la instalación, de forma que para una cierta temperatura predeterminada en el bulbo, todo el líquido se vaporiza quedando en el bulbo vapor saturado. De esta forma cualquier aumento de temperatura que se tenga en el bulbo (sobrecalentamiento adicional) tendrá un efecto muy pequeño en la presión del bulbo. Al limitar la presión que pueda ejercer el bulbo, como el equilibrio de la válvula es establecido sólo cuando la presión en el bulbo es igual a la presión en el evaporador más la presión ejercida por el resorte (siendo constante ésta última), llega un momento en que la suma de las presiones del evaporador y del resorte excede al valor de la presión en el bulbo y la válvula se cerrará.
En este tipo de válvulas se han de tener las siguientes precauciones: (1) el cuerpo de la válvula debe colocarse en una zona más caliente que el bulbo y (2) el tubo de conexión del bulbo al cabezal de fuerza no debe permitírsele que roce con alguna superficie más fría que la del bulbo. De otra forma, se producirá condensación en el punto más frío y la válvula será inoperante en estas condiciones.
Las válvulas de expansión limitadoras de presión son actualmente muy utilizadas, sobre todo en aplicaciones de acondicionamiento de aire. Generalmente, la selección de un válvula limitadora de presión se hace con una presión máxima de operación de 0,35-0,71 Kg/cm2 por encima de la presión media del evaporador en condiciones de funcionamiento normal.
Cuando las válvulas de expansión tienen el bulbo cargado con el mismo refrigerante que tiene la instalación, son adecuadas para casi todas las aplicaciones de mediana y alta temperatura, pero no lo son generalmente, para baja temperatura. Esto sucede porque el sobrecalentamiento necesario para impulsar el diafragma será demasiado grande para bajas temperaturas, según se desprende del análisis de la relación presión-temperatura de cualquier refrigerante utilizado.
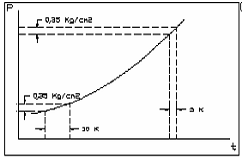
Las válvulas de expansión termostática con fluido diferente al refrigerante de la instalación, se llaman de "carga cruzada" y se utilizan en aplicaciones de temperatura baja fundamentalmente.
Cuando un evaporador tiene más de un circuito refrigerante, éste es distribuido después de pasar por la válvula de expansión y por medio de distribuidores (que a veces forman parte de la válvula). Los distribuidores pueden ser de distintos tipos.
En las válvulas de expansión termostáticas debe usarse el compensador externo cuando la caída de presión a través del evaporador se suficiente para causar una caída de temperatura de saturación mayor de 2 ºC (en temperaturas de evaporación mayores de -18 ºC) o mayor de 1 ºC (en temperaturas de evaporación inferiores a -18º C). También se tiene que utilizar compensador externo cuando existe un distribuidor (a varios circuitos) de refrigerante en el evaporador.
(4) Tubo capilar
Es el más sencillo de los tipos de válvulas de expansión o de regulación de caudal de refrigerante. Consiste en una tubería de longitud fija, de pequeño diámetro, instalada entre el condensador y el evaporador. Se emplean solamente con compresores tipo hermético, de capacidad frigorífica relativamente constante.
(5) Válvula de expansión de flotador
En los evaporadores tipo inundado (todo el evaporador contiene fluido frigorífico) se utiliza normalmente válvulas de regulación de caudal de refrigerante del tipo de flotador. La cámara del flotador puede estar o bien en el lado de alta presión o bien en el de baja presión de la instalación frigorífica
La válvula de flotador de presión alta, que puede ser instalada en un evaporador de expansión seca, o en un evaporador tipo inundado, controla indirectamente la cantidad de líquido en el evaporador, manteniendo constante el nivel de líquido en la cámara de flotador que se encuentra a alta presión. Cuando para el compresor en una instalación de este tipo, baja el nivel de líquido en la cámara de flotador, lo que hace que se cierre la válvula y permanezca cerrada hasta que nuevamente arranque el compresor. De esta forma el mayor volumen de refrigerante siempre estará en el evaporador, siendo la carga crítica para evitar sobrealimentaciones y posible paso de líquido refrigerante al compresor.
Válvulas de solenoide
Una válvula de solenoide es accionada eléctricamente, y consiste esencialmente en un bobinado de hilo conductor (cobre) aislado y de un núcleo o armadura de hierro, que es desplazado hacia el campo magnético del bobinado cuando éste está excitado eléctricamente.
La selección de una válvula de solenoide se realiza según el caudal que se desee dejar pasar a través de la válvula, no según el diámetro del tubo donde la válvula va a ser instalada. Debe conocerse también, para la selección de la válvula, la diferencia de presión máxima admisible a través de la misma y la caída de presión que tiene que producirse a través de ella
Enlaces